Teach an old battery new tricks with Battery Tracker
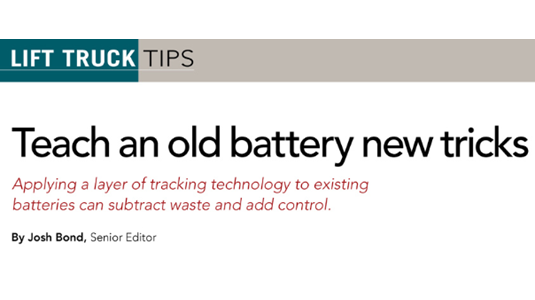
The battery room, the beating heart of a forklift fleet, should probably take a look at its cholesterol levels. In recent years, the performance and market share of electric forklifts has risen in step with battery prices, creating symptoms that prompted many to schedule battery management checkups. At the same time, the cost of electronics, sensors and transmitters of all kinds have plummeted, leading to a proliferation of battery management solutions, telematics, and fleet management technologies. According to Harold Vanasse, vice president of sales and marketing at Philadelphia Scientific, the prognosis is concerning and treatment options can be overwhelming.
“It’s a very conservative industry, and a lot of new technologies are being thrown at them,” Vanasse says. “I’m impressed and amazed with the level of technology in distribution centers, and then when you get to moving batteries, it’s back to our grandfathers’ technology.”
To be fair, those responsible for managing batteries do have an appetite for improvement. However, Vanasse says many have a hard time putting resources into a battery infrastructure that is wasteful. Their eyes are fixed on someday affording wholesale upgrades to next-generation batteries and chargers, even lithium-ion or fuel cell alternatives. In the meantime, many are falling behind.
On the spectrum between innovators and laggards in battery room management, Vanasse suggests the innovators are few and far between, maybe totaling 10%. In the middle of the curve are the 65% or so who get by. The balance is about one in four who are operating well below ideal efficiency. These are operations characterized by battery abuse and misuse, frequent changes and an oversized battery inventory. Conventional wisdom calls for three batteries per lift truck. With some management technology, it’s often possible to cut it to 2:1.
“When people talk about the promising new battery technologies, they mention things like the embedded intelligence, communication and tracking they offer,”
Vanasse says. “You can add that to a conventional lead-acid battery and products from a number of companies can readily produce a return on investment within a year. This is a measure of product quality, sure, but it’s even more a measure of the opportunity for savings.”
With battery inventory right-sized, monitoring technologies allow for continuous improvement. Vanasse notes a trend toward more data mining, where patterns in usage information help improve operation management’s understanding.
“It’s not just the innovators who have the technology and the people trained to manage that level of detail,” he says. “Others will hear about a solution that claims it can save two minutes per battery change and say, ‘who cares?’ Don’t bother me with two minutes. If you do the math on how many hundreds of changes happen in a week, it adds up to a lot of money.
Read the article and more on mmh.com